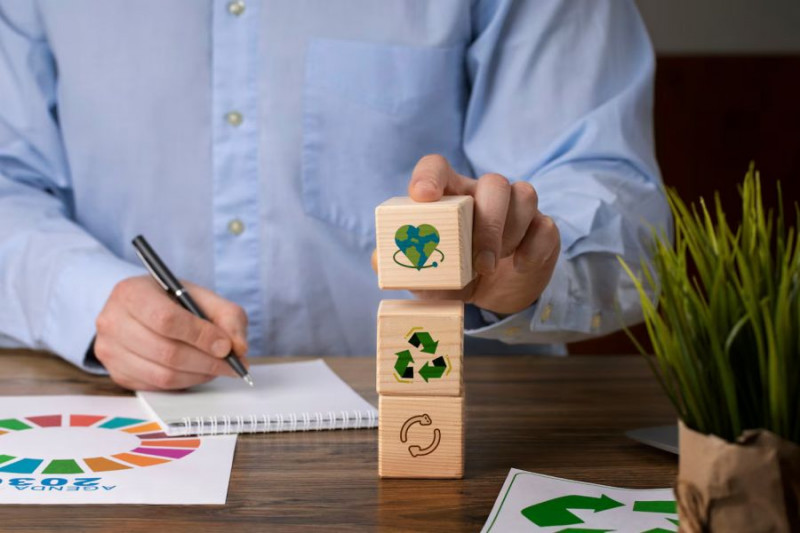
Europejski Zielony Ład i unijne przepisy dotyczące gospodarki o obiegu zamkniętym zobowiązują firmy z sektora tworzyw sztucznych do wdrażania nowoczesnych technologii recyklingu oraz usprawniania procesów produkcyjnych. Dla małych i średnich przedsiębiorstw, które stanowią ok. 90% tej branży i często dysponują ograniczonymi zasobami na inwestycje, zmiany te stanowią szczególne wyzwanie.
Branża tworzyw sztucznych to istotny element polskiej gospodarki zapewniający miejsca pracy dla 225 tys. osób. Sektor ten charakteryzuje się dynamicznym rozwojem – średnia roczna stopa wzrostu produkcji sprzedanej w cenach bieżących w latach 2011–2022 wyniosła 8,7% wobec 7,8% dla całego przetwórstwa przemysłowego. Polska produkcja, szacowana na 1,7 mln ton, nie zaspokaja krajowego zapotrzebowania wynoszącego 4,1 mln ton, co skutkuje koniecznością importu. Odbiorcą jest głównie przemysł opakowaniowy (34%), budowlany (19%) i motoryzacyjny (11%). Aby zmniejszyć negatywny wpływ na środowisko i uniezależnić się od importu surowców, konieczne jest przejście na gospodarkę o obiegu zamkniętym.
Zmiany te napędza rosnąca świadomość konsumentów, która wywiera presję na producentów. Klienci coraz bardziej interesują się tym, czy opakowania produktów, które kupują, nadają się do recyklingu. Zgodnie z wynikami ubiegłorocznego badania SW Research 92% Polaków deklaruje segregację odpadów opakowaniowych, co stanowi wzrost o 13% w porównaniu z 2023 r. Dane z „EkoBarometru” opracowanego przez SW Research i Grupę Akomex wskazują natomiast, że 69% respondentów zaczęło regularnie segregować śmieci w ciągu ostatnich sześciu lat. Ponadto 71% polskich konsumentów zastanawia się, co dzieje się z opakowaniami po zużyciu produktów, a główną motywacją do proekologicznych działań jest dla nich chęć dbania o środowisko (40%). W odpowiedzi na te oczekiwania firmy z branży tworzyw sztucznych wdrażają strategie zamkniętego obiegu surowców i poszukują innowacyjnych rozwiązań, aby minimalizować swój wpływ na środowisko.
Jak wskazuje Agnieszka Zdanowicz, wiceprezes zarządu Klastra Gospodarki Cyrkularnej i Recyklingu, GOZ jest zawsze procesem kosztownym, zwłaszcza na początkowym etapie. Poza inwestycjami w technologie recyklingowe niezbędne są m.in. zmiany w modelach biznesowych, liniach produkcyjnych i sposobach zarządzania danymi. Z danych Plastics Europe wynika, że średni czas zwrotu z inwestycji w nowe technologie recyklingu wynosi ok. 7–10 lat, co stanowi barierę dla mniejszych firm. – Tego nie da się zrobić w sposób prosty i tani, te zmiany technologiczne są drogie, podobnie jak ewentualnie potrzebne działania B+R, współpraca z ośrodkami naukowymi czy doradcami, którzy wspierają firmy i pomagają im te zmiany wdrożyć. Na wejściu to jest proces absolutnie kosztowny, te koszty są rozłożone na lata. Natomiast docelowo to ma na celu zoptymalizowanie produkcji, zamknięcie obiegu nie tylko związanego ze strumieniem surowców, ale i wszystkich innych zasobów. Dlatego to są też możliwości i w momencie, kiedy wchodzą elementy nowych modeli biznesowych, nowych produktów wytworzonych na bazie zamknięcia obiegu surowca albo użycia innego zasobu z innej firmy, w myśl GOZ-owych symbioz gospodarczych, wtedy zaczynamy mówić już o przychodzie. Natomiast to wszystko wymaga inwestycji i kosztów, nie tylko technologicznych, ale też np. osobowych – tłumaczy ekspertka.
Kolejną przeszkodą jest gotowość firm i pracowników do wprowadzenia zmian. Często potrzebne jest wsparcie specjalistów, którzy oferują optymalne rozwiązania uwzględniające indywidualne potrzeby każdej firmy. Jednocześnie jednak GOZ otwiera przed przedsiębiorstwami nowe możliwości. W perspektywie długoterminowej może prowadzić do obniżenia kosztów produkcji, rozwoju produktów z recyklingu czy generowania dodatkowych przychodów dzięki innowacyjnym modelom biznesowym opartym na surowcach wtórnych. Organizacje, które już teraz inwestują w gospodarkę cyrkularną, mają szansę na osiągnięcie znaczącej przewagi konkurencyjnej i realnych zysków w przyszłości.
fot. freepik.com
oprac. /kp/